STN Co.,Ltd
Welding Power Source Integrated Robot TAWERS (S-AWP) and Handling Robot
Achieving Advanced Automation! Enhance Productivity and Create a Comfortable Workplace with S-AWP.
Introduction: 2017 Location: Ibaraki
Issue
STN Co., Ltd. manufactures agricultural machinery parts requiring extremely high welding quality. To reduce welding defects caused by workpiece variation and increase productivity, it was necessary to achieve a high level of welding technology standardization.
Solution
The stable arc and wide condition tolerance of S-AWP allowed it to handle gap welding caused by workpiece precision variations, achieving highly efficient and high-quality welding results. The spatter reduction effect was also significant, reducing the workload in subsequent processes.
"The wide condition tolerance for workpiece gaps and solid penetration were impressive. We were able to increase production efficiency by reducing the number of passes required for welding gaps of 3-5mm."
Background
High-Quality Product Production and Safety as Challenges
STN Co., Ltd., which counts major agricultural machinery manufacturers among its clients, is optimizing the entire manufacturing process. This includes designing and manufacturing jigs in-house to create equipment tailored to the production site. Addressing the needs for "providing high-quality products to customers" and "ensuring a safe manufacturing site" made the ease of equipment design, high-level welding standardization, and creating a safe workplace crucial points.
Initiatives for Creating a Comfortable Factory
Securing skilled welders is a challenge, but so is attracting younger workers. To change the dark image commonly associated with factories, STN has undertaken various initiatives. Rather than simple labor-saving, creating a workplace where employees can work with a smile and improving individual productivity was one of their goals.
Reason for introduction
“Stable Welding Quality" Achieved with Ultra-Low Spatter
They repeatedly changed gases and materials to reduce spatter, but found that the S-AWP welding method significantly reduced these efforts, proving effective for spatter reduction and productivity improvement. This was a major point for introducing S-AWP.
“Seamless Integration" of Panasonic Robots' Versatility
"Panasonic robots are highly versatile in terms of electrical specifications, making equipment design easy" (Minoru Watanabe). Using robots allowed even non-technicians to manufacture products and quickly provide high-quality products to customers, which was also a crucial point for introducing robots. The high versatility in electrical specifications made Panasonic robots the unanimous choice, allowing for fully automatic welding process design.
Post-introduction effects
Significant Increase in Manufacturing Process Automation
As they advanced towards full automation of welding, labor-saving, which was a major challenge, progressed. Especially by coordinating with Panasonic's handling robots for transporting heavy objects and welding workpieces, human labor was significantly reduced, achieving a high level of automation. This greatly contributed to productivity improvement and gradually realized STN's goal of a “comfortable working environment" for workers.
Reduction in Costs and Realization of Human Resource Development
Previously, they used robots from other manufacturers, but faced challenges with increasing inventory costs for repair parts and internal human resource development. Since standardizing on Panasonic robots, they have reduced inventory costs and are highly satisfied with after-sales service, including error handling. The unification under one manufacturer also facilitated knowledge sharing regarding robot operation and settings, promoting high-level human resource development.
Significant productivity improvement achieved by multiple robots operating simultaneously.
Handling robots smoothly transport workpieces to each welding process.
Improved teaching skills of workers contribute to high efficiency and high-quality production.
Minimal spatter adhesion with a good bead appearance on thin plates.
High-quality welding results achieved on medium-thick plates with stable welding effects.
STN engineering meetings support line and jig design concepts.
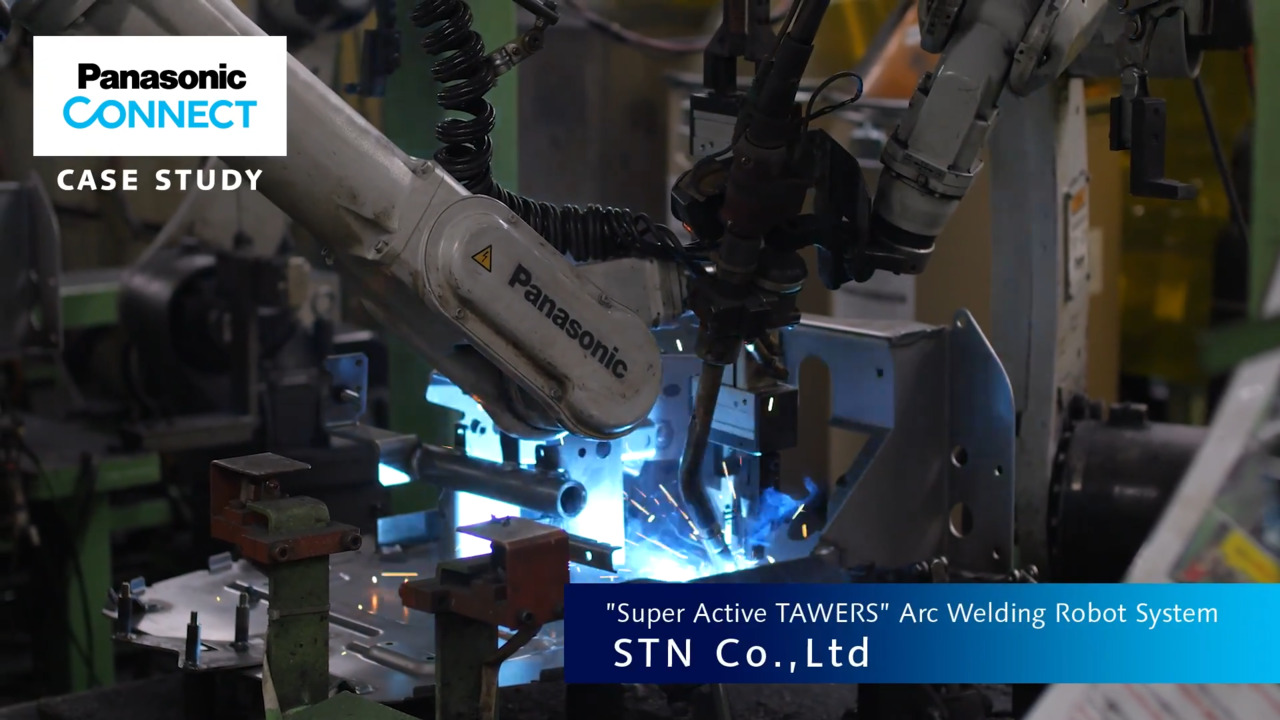
Equipment supplied
Welding Power Source Integrated Robot TAWERS (S-AWP specifications) and various types of handling robots
Voice of customers
"We've achieved low spatter even on thick plates that are prone to spatter, reducing working hours by 25%, including finishing processes. Automating difficult tasks has also created a safer workplace, promoting work style reform and making it easier to attract workers. Customers also appreciate the ease of placing orders with STN."— Minoru Watanabe,CTO, STN Co., Ltd.
Outstanding Welding Performance and Versatility
Due to the improved performance of the robot controller, even those with little welding knowledge can teach welding robots. Additionally, the use of laser sensors enables easy identification of similar workpieces and inspection of parts before welding, highlighting the versatility of Panasonic robots.
Customer introduction
STN Co., Ltd. has production bases in Ibaraki Prefecture and the USA, manufacturing various functional parts, including tractor handle parts and bonnet internal components. Their integrated manufacturing system for press processing, laser processing, bending, welding, and product processing produces high-quality products with short lead times.
Click here for a quotation of the Welding Power Source Integrated Robot TAWERS
Support
Global network
Panasonic has established a system to support customers all over the world. Customers expanding production from Japan to overseas factories can also use our equipment with peace of mind.
Website for Panasonic Shoyokai
Website dedicated page for members of Panasonic Shoyokai. You can download the application form to join the membership website P-Web.