Kaga Factory, Panasonic Connect Co., Ltd.
Remote Laser Welding Robot System LAPRISS
High-quality welding without relying on individual skills achieved by a productivity improvement solution using LAPRISS
Introduction: March 2020 Location: Ishikawa, Japan
Issue
Since some welding processes require special skills, the processes had to be outsourced to a specialized external factory with skilled workers.
Solution
Panasonic Kaga Factory achieved high-quality welding with minimum post-welding treatment by installing the laser welding robot LAPRISS for in-house welding. They also successfully reduced costs by approximately 40%.
"With laser welding robots, we achieved a welding process that does not rely on human skills. This is also part of efforts to solve the labor shortage, which is one of social issues."
Background
To establish production processes that do not rely on humans' special skills and contract factories where employee turnover is high
The Kaga Factory produces consumable parts as well as torches and other peripheral equipment for welding. In addition, it has machining, sheet metal working, welding, and coating processes. The processes requiring special skills, including the welding of thin plates, had to be outsourced to operate the factory. However, nor is it easy for contract factories to continuously secure highly-skilled welders due to the high incidence of employee turnover at. Therefore, the Kaga Factory introduced LAPRISS in order to achieve high-quality welding without relying on human skills. (Mr. Kadono, Plant Superintendent)
Reason for introduction
To avoid personnel-related risks at contract factories to maintain production processes where everyone can manufacture good products
Thin plate welding is a process that requires special skills to control heat distortion and burn-through. It is also difficult to secure such skilled workers at contract factories, where workers may be older or less likely to stay at the same workplace for a long time. We decided to install LAPRISS at the Kaga Factory to ensure consistent, high-quality welding. (Mr. Yamada, Production Section)
To promote our products to customers by using them at our factory
Since the Kaga Factory has a welding process, we also face similar issues as our customers' at our own welding site.
Another reason we introduced LAPRISS was to help customers facing similar challenges. We had already installed our own arc welding machines and welding robots in our factory. We decided to install the laser welding robot LAPRISS as well because we wanted to promote its benefits to our customers. (Mr. Kadono, Plant Superintendent)
Benefits of introduction
Establishment of a high-quality production process, requiring only the setting of workpieces and pressing of a button
The greatest benefit of LAPRISS is that it enables a production process that does not rely on special skills. At a contract factory, welding required a series of processes, including tack welding, final welding, finish work, and heat distortion removal. Now we simply set the workpieces and press the button to complete the welding process. Manufacturing often relies on special skills and expertise of humans; however, considering social issues such as business continuity and labor shortages, this effort to replace human operations with the state-of-the-art equipment was significant. (Mr. Yamada, Production Section)
Beautiful bead appearance only achieved through laser welding
High welding quality is also achieved with beautiful finish only achieved through laser welding. After coating, the finish is so impressive that it is impossible to tell whether the components were bent or welded. (Mr. Yamada, Production Section)
Reduced lead times as well as costs
We were able to reduce costs by approximately 40% by working on in-house welding.
In-house welding has also reduced lead times, compared to those required by contract factories, which are now three to four days. The required stockpiling was thereby reduced as well. (Mr. Yamada, Production Section)
The Kaga Factory is using two sets of LAPRISS laser welding robots. Although the heat input is low, water-cooled jigs are also used to minimize heat distortion.
Workpieces welded by LAPRISS. A smooth and very beautiful bead appearance.
Appearance of workpieces after coating. The finish is so beautiful that it is impossible to tell at first glance whether the components were bent or welded.
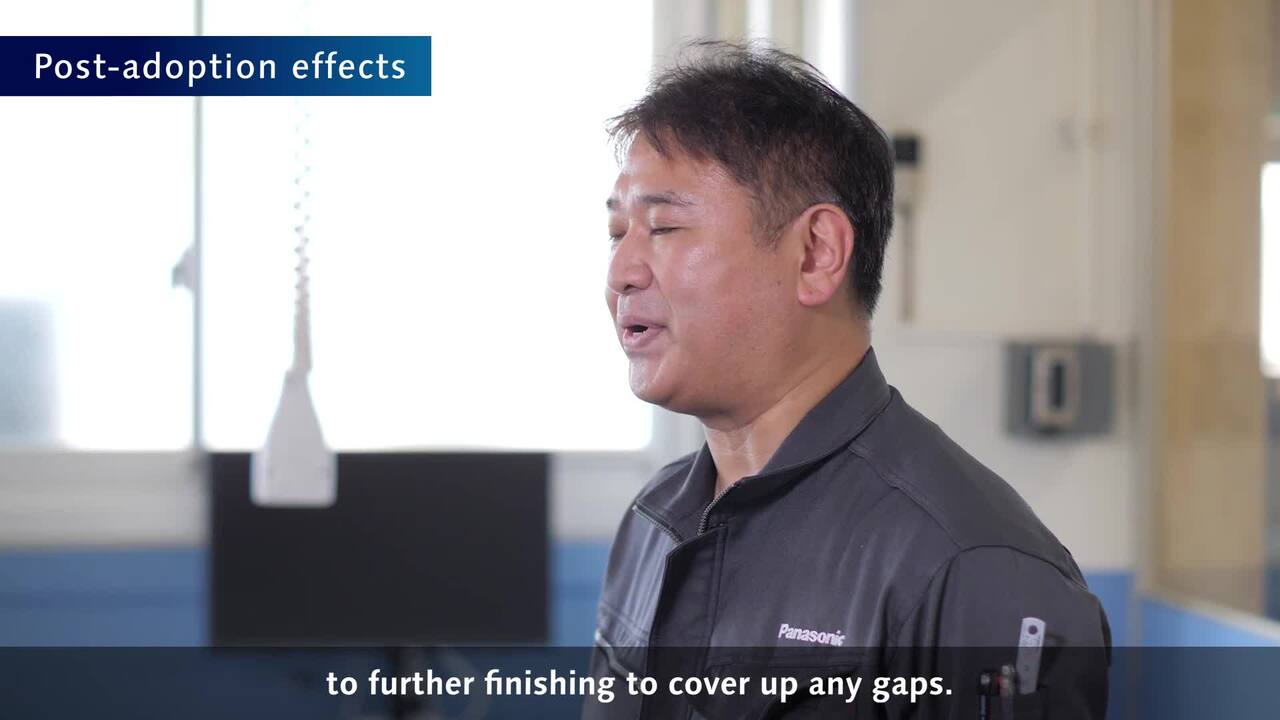
Equipment supplied
Two sets of Remote Laser Welding Robot System LAPRISS
Future prospects
Improving welding quality as well as management through connection
Although LAPRISS is currently not connected to our iWNB (Integrated Welding Management System) visualization software, we are hoping that it will be connected to manage the overall welding process in the future.
In addition, the improvement of welding quality may also enable us to expand the scope of our work and improve the production yield, thereby reducing waste materials. We are hoping to work on these areas in the future.
Everyone can manufacture the same products by simply pressing a button
Although launching LAPRISS was difficult, we are now able to produce the same high-quality products simply by pressing a button once workpieces are set. In the future, we would like LAPRISS to make further contributions by expanding its application to a wider range of models.
Customer introduction
Kaga Factory, Process Automation Business Division
Established in 1974, the Kaga Factory produces consumable parts as well as torches and other peripheral equipment for welding. Like our customers, the factory has processes from sheet metal working to welding, coating, and assembly. The factory uses our own products from the same perspective as our customers, and promote activities to propose improvements to them.
Support
Global network
Panasonic has established a system to support customers all over the world. Customers expanding production from Japan to overseas factories can also use our equipment with peace of mind.
Website for Panasonic Shoyokai
Website dedicated page for members of Panasonic Shoyokai. You can download the application form to join the membership website P-Web.