Kaga Factory, Panasonic Connect Co., Ltd.
iWNB (Integrated Welding Management System)
The cycle time has been reduced by visualizing the welding process, which is difficult to see. Improvement solution by using iWNB.
Introduction: October 2020 Location: Ishikawa, Japan
Issue
The factory was unable to maintain efficient welding process operations in the locations where welding robots were used. The quality and quantity of information on the outsourced processes was also limited, placing a heavy burden on site managers due to difficulties in operation analyses.
Solution
The welding robot process was visualized by introducing iWNB. Checking information regularly maintains improvements, achieving a 15% cycle time reduction.
"Information on welding robots comes through iWNB, which is a major advantage in terms of management, and it also reduces the workload of site managers."
Background
To receive accurate information about the increasingly outsourced production processes
Mr. Kadono, Plant Superintendent, says that the Kaga Factory increasingly outsources production, and sometimes, they do not receive any reports from contract companies unless a serious problem has occurred. It is often the case that they are not provided with any information about worksites. Under such circumstances, even if they wanted to improve production processes, it was difficult to know what to improve and how.
Reason for introduction
The welding process was not visualized with data, so we could not take any specific actions to bring about improvements
We introduced iWNB because we believed that the visualization of equipment data would enable us to identify the causes of variations, leading to reduced losses. We also believed that the visualization of welding robot errors and short production stoppages would help us reduce the average cycle time. (Mr. Teruta, Factory Management Section)
To promote our products to customers by using them at our factory
We also installed iWNB because we wanted to understand how customers can actually use the product at their factories to reap its benefits, by monitoring its performance at the Kaga Factory, which is not a large factory. We wanted to use the system's functions at our own factory and propose our use cases to our customers, including a maintenance information management function for a factories with many robots, and a traceability function for those that require traceability. (Mr. Teruta, Factory Management Section)
Benefits of introduction
Narrowing down problem locations has significantly increased the PDCA cycle speed
By checking the iWNB's error history, we can visualize which models had frequent errors and at what timing. Because we can narrow down the location of the cause of the problem, we have significantly increased the speed of the PDCA cycle for improvements. (Mr. Teruta, Factory Management Section)
Visualization with the on-site camera solution reduced the cycle time by 15%
The on-site camera solution uses fixed-point cameras to check the movement of workers at any given time. This camera solution enabled us to identify wasteful and uneven human movements and achieve a 15% reduction in cycle time by improving the movements. (Mr. Teruta, Factory Management Section)
Reduced workload of process managers and operators
Improving production itself is not difficult. Making continuous improvements is difficult. I believe that receiving information on welding robots through iWNB is helping us to reduce the workload of process managers. The camera solution is used for making improvements, not for placing workers under surveillance. Our contract companies understood that the solution would facilitate their work, and iWNB also improved communication with them. (Mr. Kadono, Plant Superintendent)
The Kaga Factory introduced iWNB to promote visualization of the welding processes that use welding robots. Improvements are continuously made by checking the results against the target cycle times
A camera solution to monitor and improve worksites. Linked to iWNB, it allows the data to be used for analyzing factors other than welding conditions.
A screen showing images achieved through the integration of iWNB and the camera solution. The cause of an anomaly can be identified by understanding what was happening at the worksite through video.
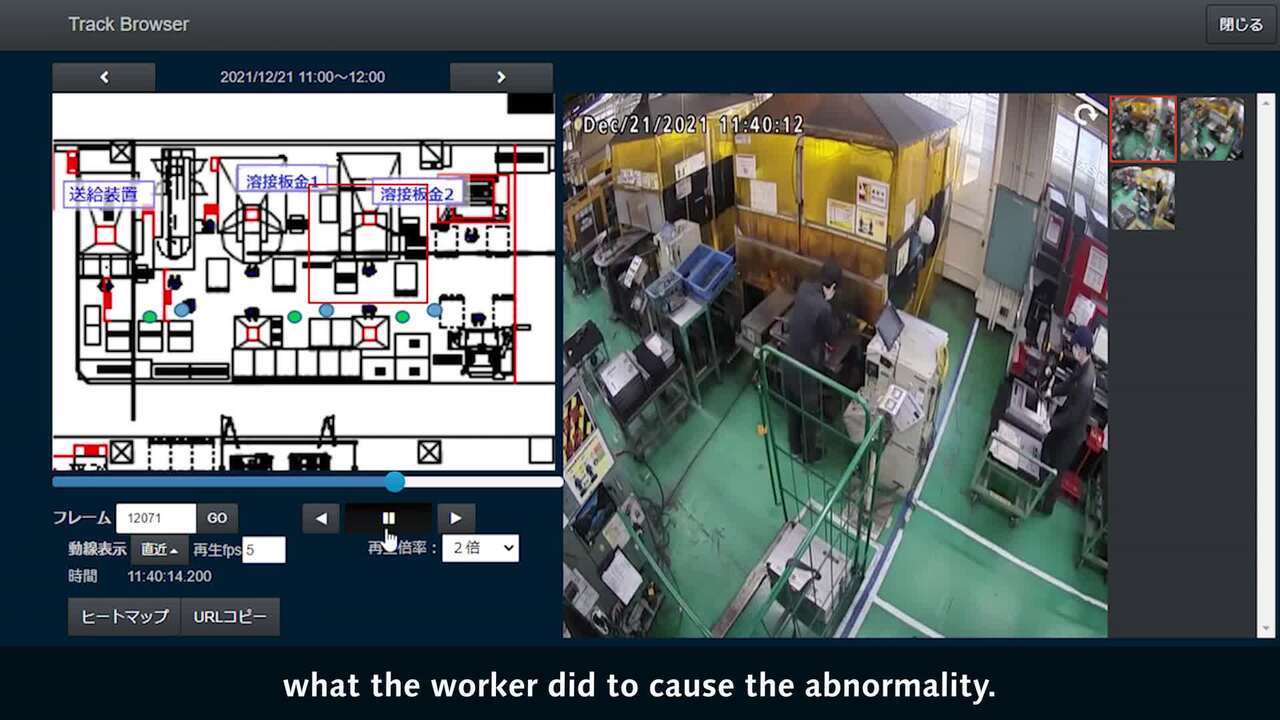
Equipment supplied
iWNB (Integrated Welding Management System) and an on-site camera solution
Future prospects
We want to improve the functions that may not be currently customer-friendly.
As users of iWNB as well as colleagues of the development team members, we can make tough demands on them for improvement (laughs). We would like our feedback to help improve Panasonic welding system products so that they will be more satisfactory for many customers.
We would like to contribute to solving our customers' challenges from the perspective of our small- and medium-sized customers
The Kaga Factory serves as a showcase facility where we actually use welding-related products and solutions manufactured by our business division. If any of our customers would like to see a case study, I strongly recommend to have look at our use case.
Customer introduction
Kaga Factory, Process Automation Business Division
The Kaga Factory was established in 1974. It produces consumable parts as well as torches and other peripheral equipment for welding. Like our customers, the factory has processes from sheet metal working to welding, coating, and assembly, and uses our products from the same perspective as our customers, giving feedback for improvements to our products.
Support
Global network
Panasonic has established a system to support customers all over the world. Customers expanding production from Japan to overseas factories can also use our equipment with peace of mind.
Website for Panasonic Shoyokai
Website dedicated page for members of Panasonic Shoyokai. You can download the application form to join the membership website P-Web.