Maruo Kousakusho Co., Ltd.
Welding Power Source Integrated Robot TAWERS (S-AWP)
A solution to a new level of productivity improvement for welding sites using the S-AWP technology
Introduction: December 2020 Location: Osaka, Japan
Issue
The spatter removal process after welding was time-consuming and required many workers.
Solution
Ultra-low spatter welding was achieved by installing the optional S-AWP technology to the welding robot TAWERS. They could reduce the time spent on spatter removal by more than 90%.
"Panasonic robots have helped us maintain our priority of meeting deadlines and delivering quality products."
Background
Meeting the increasing production volume and required welding quality
Maruo Kousakusho, a major manufacturer supplier, was spending a lot of time and effort on removing spatter, which required many workers. In addition to the required time and effort, this spatter removal also resulted in robot stoppages. Moreover, as end users have increasingly demanded higher quality products in recent years, the company was seeking a welding method that could achieve both high-speed production and high-quality welding. They focused on the S-AWP technology and introduced S-AWP, which would enable high-quality welding with high speed and low spatter.
*Spatter: Spatter refers to the small droplets of molten metal that are scattered during welding (sparks). Low-spatter welding is required because once spatter has settled on the base metal, it is difficult to remove.
Reason for introduction
Experiencing the benefits of ultra-low spatter welding with the S-AWP technology
The S-AWP technology is a welding method unique to Panasonic, which not only achieves the wire feed of the conventional welding process, but also enables the welding wire to be fed continuously with a back and forth motion, achieving ultra-low spatter welding. Maruo Kousakusho welds a wide variety of workpieces, ranging from thick to thin plates. Because thick-plate high-current welding in particular generates a large amount of spatter, the company was impressed by the significant reduction in man-hours required to remove the spatter. Mr. Sawa, who is working on site, stated, "Now we do not have to worry about removing spatter. Our work has become extremely efficient.
Reliable repair and support system
The company has 36 welding robots and all of them were made by Panasonic. Some of them have been used for about 20 years. The reason for this can be attributed to Panasonic's repair and support system. "We called the Panasonic service center the other day when we had a welding problem, and Panasonic staff promptly offered their support on the same day." They say that a reliable repair and support system is essential for meeting their deadlines and maintaining welding quality.
Benefits of introduction
The low-spatter welding method allows us to work without stopping the robots
The benefits of using S-AWP have been significant. For example, when compared to conventional welding methods, much less spatter is generated, eliminating the need for a spatter removal process. The time spent removing spatter can now be used in a more productive way, such as for setting up subsequent workpieces. The introduction of the S-AWP technology has also made it possible to achieve thin-plate welding with a beautiful finish. In particular, the requirements for beads are very strict for exterior parts. Once welding fails, it becomes a big loss. Thanks to the welding by S-AWP, our productivity has improved.
Easy operations reduce operators' workload
Compared to other companies' welding robots, TAWERS's teach pendant is easy to use , allowing anyone to achieve stable and high-quality welding even if they have no experience with manual welding.
A total of 36 Panasonic robots operate throughout the two factories.
Workpieces welded using the S-AWP technology
The latest welding robot S-AWP (optional)
Thick-plate parts for agricultural machinery
Inspection of welding quality
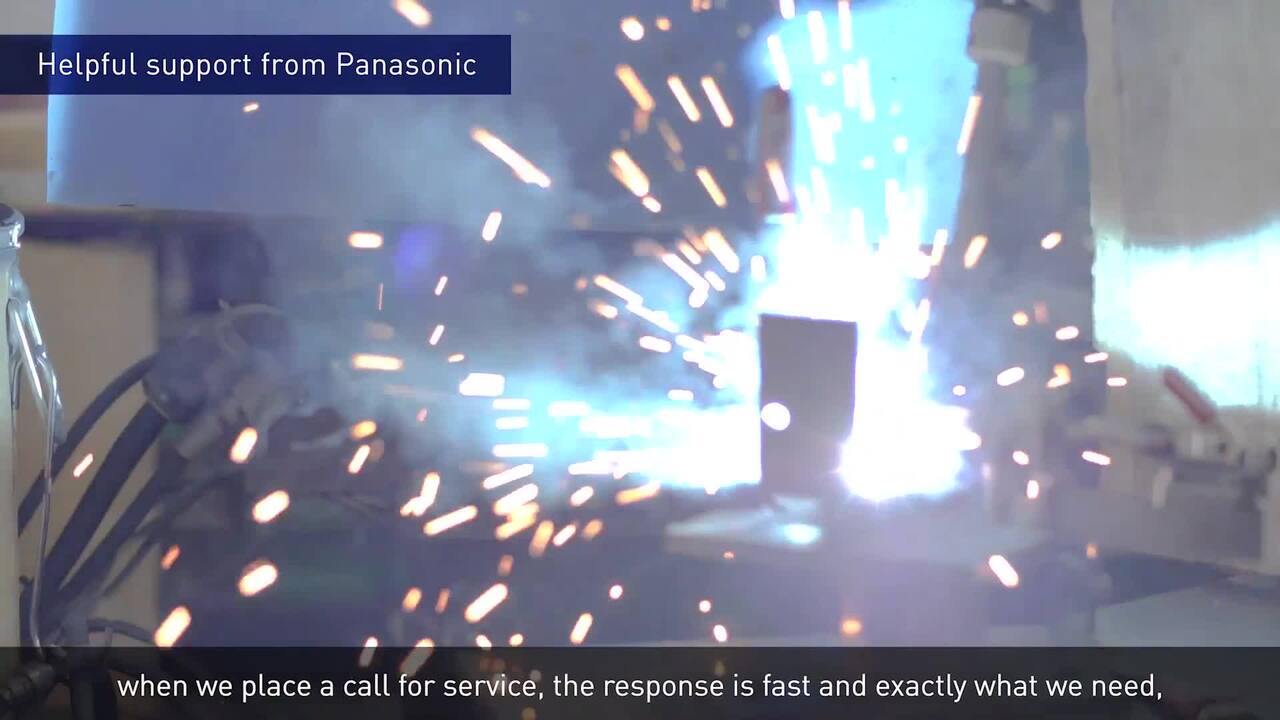
Equipment supplied
Welding Power Source Integrated Robot S-AWP (optional)
Voice of customers
Meeting deadlines and improving quality
The installation of S-AWP has minimized the variations in weld appearance as well as increased the production volume. I can see the significant evolution of welding robots in S-AWP, which generates less spatter. Our priorities are meeting deadlines and ensuring quality, with particular emphasis on quality. We would like to continue using Panasonic welding robots in a proactive manner. (Mr. Yasunobu Maruo)
Experiencing impressive evolution
Following the installation of S-AWP, the time spent on removing spatter has been reduced by about 90%, and of course, scratches on the workpieces caused by the spatter removal work were also eliminated. We are fighting over the robots (laughs). I am impressed by the evolution. (Mr. Tatsuya Sawa)
Customer introduction
Prioritizing meeting deadlines as well as quality
Maruo Kousakusho Co., Ltd. was established in 1972. The company produces parts for tractors, construction machinery, and agricultural machinery, as well as construction metal fittings and medical bed parts. With deadlines and quality as top priorities, the company is proactively introducing robots to achieve these goals.
https://maruo55.co.jp/
Click here for a quotation of the Welding Power Source Integrated Robot TAWERS
Support
Global network
Panasonic has established a system to support customers all over the world. Customers expanding production from Japan to overseas factories can also use our equipment with peace of mind.
Website for Panasonic Shoyokai
Website dedicated page for members of Panasonic Shoyokai. You can download the application form to join the membership website P-Web.