CANYCOM
Welding Robot TAWERS
Speedy production start-up! Productivity improvement solutions using off-line teaching.
Introduction: 2021 Location: Fukuoka
Issue
(1) Equipment had to be stopped during teaching, which meant that teaching was often a nighttime operation, placing a burden on the work site.
(2) It was necessary to create a system that could handle increased production.
Solution
Off-line teaching software "DTPS III" is used to create teaching programs on a PC without stopping robot operation. As a result, the company was able to speed up the start-up of production and cope with the planned increase in production volume.
“The night shift work just for teaching has been eliminated and the workload has been lightened. Using DTPS, we can now create teaching programs with simple operations.The technical training for service personnel has also been very helpful."
Welding Group Manager Takao Kusano
Background
Need for high-mix low-volume production
CANYCOM, a manufacturer of work vehicles for agriculture and construction, produces 50 models with 200 specifications, and its main products have more than 300 different parts per unit.
With the increase in the number of units manufactured, the welding process became a bottleneck in the lead time required to ship finished products.
“The number of products supplied is directly related to how much welding can be done in a day. When we launched the new plant, we set a goal of producing 1.5 times as many products as the previous plant and decided to install a robot system with multiple welding robots as a solution for high-mix low-volume production."
(Mr. Kusano, Welding Group Manager, Production Department)"
Reason for introduction
(1) Minimize production downtime
In order to minimize the downtime of welding robots, one of the key points was to introduce a system that enables off-line teaching* concurrently with equipment operation.
Another factor in their decision was the ease of managing program data with DTPS III*, as new models are launched every year.
Off-line teaching: A method of programming robot movements using simulation software on a computer, without using the actual robot.
DTPS III: Panasonic's offline teaching software
(2) High Speed and High Quality Welding
The S-AWP technology has excellent arc follow-up stability during high-speed welding, enabling a significant reduction in welding time per workpiece manufactured compared to other companies' products.
In addition, the amount of spatter generated was very low, which was an advantage in terms of work efficiency considering the spatter removal process during and after welding.
“We compared our robot with robots from other manufacturers, but the Panasonic robot was the only one that could achieve our target takt time." (Mr. Kusano, Welding Group Manager, Production Department)
(3) Support when problems occur
“I was impressed by the fact that Panasonic made it easy to get in touch with service personnel and sales staff when problems occurred, and they were able to get to us immediately.
We have been using Panasonic equipment for a long time, but we have rarely had to stop due to equipment trouble for a long period of time. (Mr. Kusano, Welding Group Manager, Production Department)"
Post-introduction effects
(1) Smooth transition from start-up to production
In high-mix, low-volume production, the key to success is "how quickly can we get up and running" at the time of production changeover.
The introduction of the robot system and off-line teaching software greatly improved the start-up flow.
Without stopping operation of the actual robot, a program is created on a PC, and then the program is transferred to the robot. After that, start-up is completed simply by checking the robot's operation and making minor modifications on site.
This has greatly reduced the workload on site.
We also use DTPS (off-line teaching software) for minor program changes. I had no experience using CAD software before, but Panasonic service personnel provided me with training on its operation, and now I am very familiar with it.
(2) Production tact time per workpiece reduced to 1/3
In addition to the faster welding speed achieved by S-AWP Welding, the new robot system uses two robots, resulting in a significant improvement in production takt time.
In the past, it took 60 minutes per frame part to weld, but this tact time has been reduced to 20 minutes.
In addition, the amount of spatter generated by S-AWP Welding is also small, so the overall work time, including the spatter removal process, has been greatly reduced, much to the delight of our on-site personnel. (Mr. Kusano, Welding Group Manager, Production Department)"
DTPS III operation image. Even those who originally had no experience in operating CAD data can now perform the teaching in less time.
The system incorporates two newly introduced robots. Teaching is performed offline.
Body frame welded using the S-AWP Welding Process. The high weight and many welding points required a large system.
Bead surface welded by S-AWP Welding Process.
Parts assembly process. Canycom manufactures a wide range of products, including 50 models and 200 specifications.
A riding mower awaits shipment after inspection.
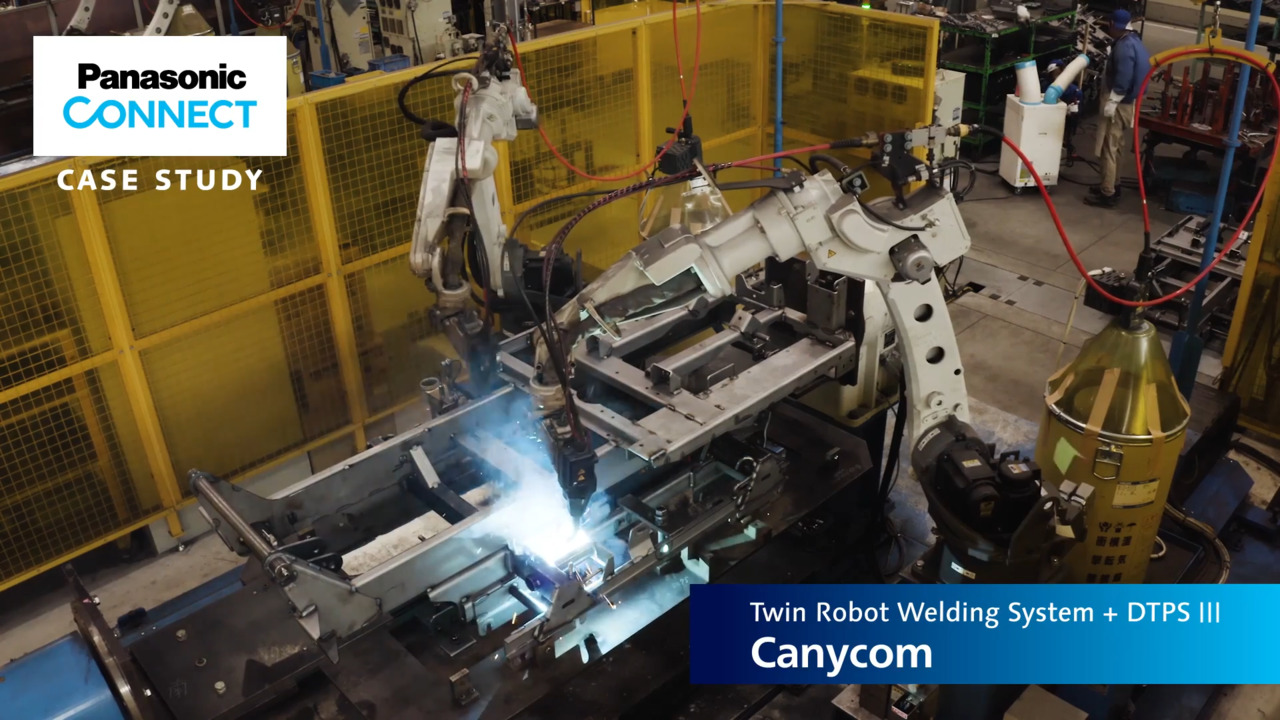
Voice of customers
Making Tedious Teaching Tasks Easier
Traditionally, teaching programs were created using the actual robot. As a result, teaching was typically handled during night shifts when the equipment was shut down. However, after the introduction of the offline teaching software DTPS, it became possible to create programs even during day shifts, which has been greatly appreciated on the production floor.
With DTPS, programs can be created with simple operations, and if there's anything unclear, our servicemen provide guidance. Additionally, we are extremely satisfied with the quality aspect. Panasonic's S-AWP technology produces minimal spatter, so much so that even the on-site operators have been asking, "Can we switch all the robots to S-AWP ones?"
Experience Remarkable Evolution
Through the introduction of welding robots, we aim for "Manufacturing that anyone can create."
To handle the production of 50 models with 200 different specifications, we were searching for welding equipment capable of supporting high-mix, low-volume production. That is when we discovered Panasonic's robots.
The "welding process" is a crucial factor in our manufacturing. Moving forward, we plan to expand the introduction of robots and link it to the growth of our company.
Customer introduction
Under the Slogan "Manufacturing is Like Enka"
CANYCOM was founded in 1948. Since then, the company has delivered numerous products worldwide, such as mowing vehicles and agricultural transporters, tailored to "the individual needs of each customer."
The slogan "Manufacturing is Like Enka" is derived from the roots of Enka music, where singers perform songs based on the requests of each listener.
Support
Global network
Panasonic has established a system to support customers all over the world. Customers expanding production from Japan to overseas factories can also use our equipment with peace of mind.
Website for Panasonic Shoyokai
Website dedicated page for members of Panasonic Shoyokai. You can download the application form to join the membership website P-Web.